BONE Structure: Sustainable recycled steel from cars for buildings
BONE BUILDING — Modern, trendy and sleek, the BONE home ensures up-to-date contemporary design in addition to sustainability and durability. “Once your concept is finished, you move into the schematic phase of ‘proving out’ the engineering and make changes that need to be made,” said Michael Melamed, BONE Structure’s US-West Director of Sales. Photo courtesy of BONE Structure.
Zero dollars. That’s how much money Stanford professor Mark Z. Jacobson tweeted he had paid for his electric, natural gas and gasoline bills after one full year of living in his Palo Alto home. Under the sleek, modern architecture of the building lies not the expected traditional wood but instead a sturdy framing of prefabricated steel, setting the quality of the building’s longevity and energy efficiency far from its peers: these are all benefits of Jacobson’s BONE home.
First founded in Canada, BONE Structure has steadily begun to expand into the American market, finishing its first-ever home in California in 2016. In the six years that BONE has been active in the California market, the company has already constructed over a dozen homes in Palo Alto alone. The company currently has active projects throughout Menlo Park, Atherton, Palo Alto, Los Gatos and Los Altos.
For BONE, the Bay Area is a prime location for expansion as a hub of innovation and technology.
As the demand for new and environmentally friendly changes is on the rise, BONE Structure aims to take hold of the opportunity presented in California and improve the traditional methods of construction.
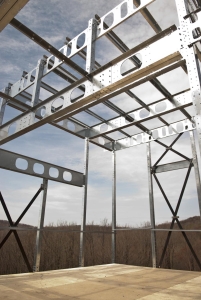
“There’s just more of an appetite [in Palo Alto] for technology, for innovation, for things that are a little different than the norm, particularly when they come with the performance that Bone structure homes do,” said Michael Melamed, a BONE Structure Director of Sales.
As an award-winning innovative family-owned company, BONE implements a unique steel construction system to help their clients design and create sustainable residential and commercial structures.
“He [BONE Structure founder Marc Bovet] saw a potential problem and a potential fix,” Melamed said. “The problem being more or less how we’ve been building homes the same way for hundreds of years, with wood framing and the same technologies.”
Using his network and experiences as part of the aerospace industry, Bovet set out to improve traditional construction methods into something more energy-efficient and high performing.
BONE found the answer through steel. More specifically, the implementation of recycled steel framing for buildings that are easily assembled during construction.
“89% of the steel that we use for our homes, which is predominantly in the framing of the home, is from recycled steel,” Melamed said.
Prefabricated and planned to fit exactly where it’s meant to go, this steel system prevents additional cutting or waste of wood.
The efficient assembly-type process, in contrast to traditional wood framing, also increases the overall efficiency and speed of the building process.
“Even though we’re using steel, you don’t see a lot of welding going on,” Melamed said. “We really talk about assembly. Instead of having all the tools, in many respects, we talk about the opportunity to just be able to have your electric screwdriver, a socket fitting, and bolt in a screw, and put the home together.”
This precision with the construction system contributes to the increased insulation of buildings and helps to improve the longevity of homes, fighting against moisture, rot, bugs, and even natural disasters. Furthermore, all BONE homes are eco-friendly and are Net Zero Energy, meaning the energy produced by the building is equivalent to the energy consumed.
“If we can get others to lean into potential solutions to build homes more quickly, that would be great,” Melamed said. “Particularly when it comes to a product like ours that is more sustainable, energy-efficient, helps homes reduce energy usage, and is fully NET zero-compliant and high performing.”